Fully Automatic High Frequency Clamper Panel Production Line
Leabon Fully Automatic High Frequency Clamper Panel Production Linee Main Features:
1. It mainly uses wood mold forming technology, hydraulic press forming technology and high-frequency heating principle to properly laminate and bend the wood, and quickly connect and press with glue to form personalized activities. This kind of production equipment is used more frequently in the field of furniture production.
2.With the feature points of high efficiency and automation, a production line often only needs one person to operate. There are automatic feeding tables and discharging tables, which save labor and labor. The overall synthesis step has an integrated feature, which can be quickly connected and air-dried. The technology is highly mature and can achieve “three provinces”, namely, glue saving, material saving, and labor saving.
3.It is more suitable for making large-area solid wood furniture, such as door panels, wardrobe panels, dining table panels, etc. When you cannot find enough solid wood raw materials, high-frequency splicing can be used to make large-area wood panels with sufficient hardness and strength. In the production process, it can be freely designed in terms of thickness, width, width, length, and length, and some wood scraps can also be used reasonably, which reduces the waste of wood, saves various funds and saves raw materials, and has environmental protection value.
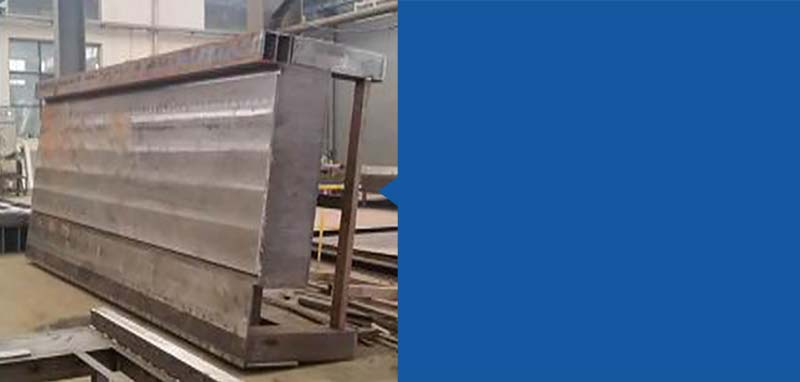
The rack adopts a pentahedron machining center, which is finished in high quality
The high-frequency part is provided with a separate cabinet, which is safe, convenient and reliable for
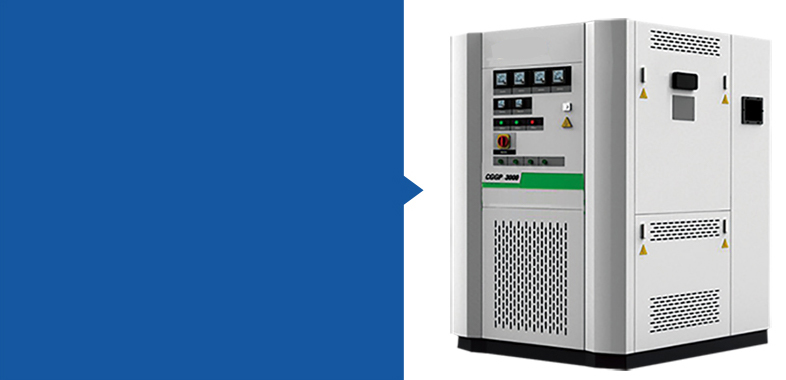
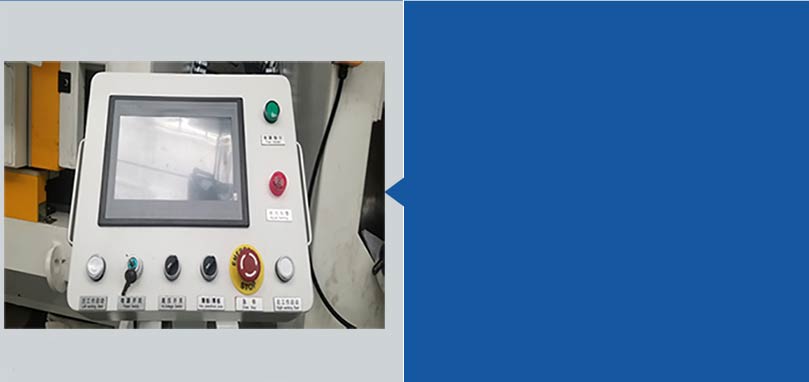
Complete software functions, friendly interface, fully automatic adjustment of heating current, system upgrade, remote control
Introduction
Fully Automatic High Frequency Clamper Panel Production Line, designed to revolutionize the field of furniture production. Our production line is built using advanced wood molding technology, hydroforming technology, and the high-frequency heating principle, to properly laminate and bend the wood, and quickly connect and press with glue to form personalized activities, all with the touch of a button.
Equipped with automatic feeding and discharging tables, our production line is highly efficient and requires only one person to operate, saving labor and effort. Our synthesis steps are integrated, allowing the wood to be quickly connected to air drying, making our technology highly mature and efficient. With our production line, you can save on glue, materials, and labor, with the added benefit of environmental protection.
Our production line is particularly suited to making large-area solid wood furniture, such as door panels, wardrobe panels, and dining table panels. When not enough solid wood raw materials are available, our high-frequency splicing technology offers an effective solution for making large-area wood panels with sufficient hardness and strength. Plus, with the freedom to design your boards according to thickness, width, length, and more, our production line is perfect for creating customized, bespoke furniture.
Featuring a range of advanced technologies, our Fully Automatic High Frequency Clamper Panel Production Line ensures the ultimate precision and accuracy when it comes to feeding and arranging single or multiple wooden strips. Using our state-of-the-art automatic board arrangement machine, a single wooden strip can be turned 90 degrees to create a perfectly pre-arranged board, all while saving more than 20% on glue usage and improving the flatness of the board.
We're passionate about bringing innovative solutions for furniture production. Our Fully Automatic High Frequency Clamper Panel Production Line is just one of many advanced technologies we offer. If you're interested in revolutionizing your furniture production process, contact us today to learn more.
WORKSHOP
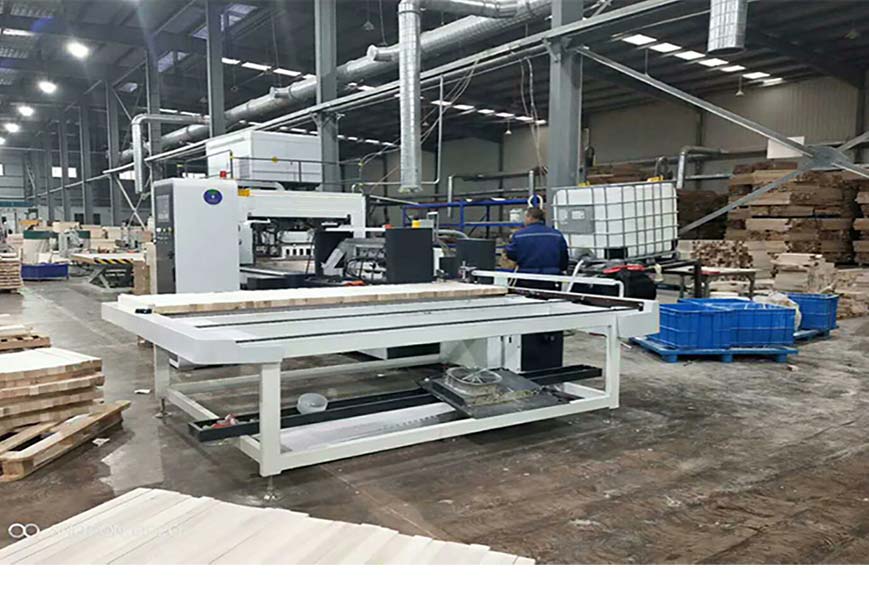
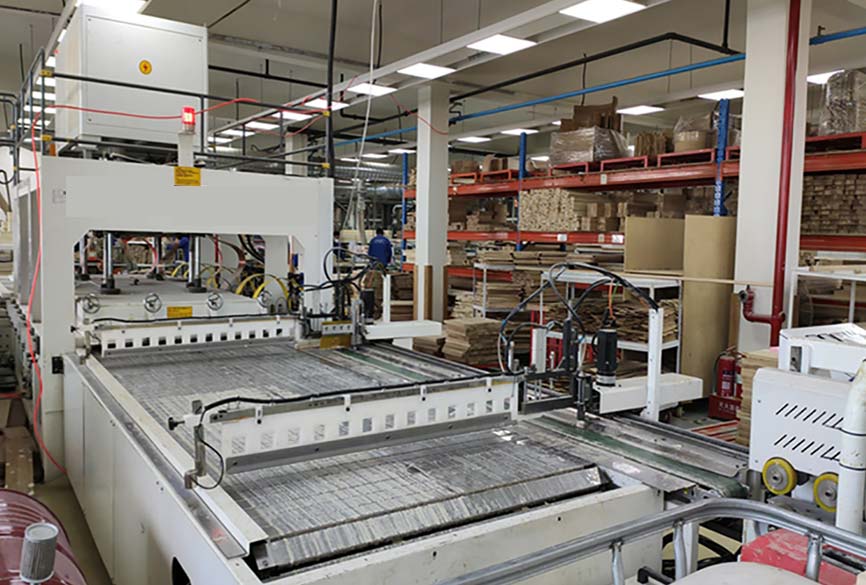
OUR CERTIFICATES
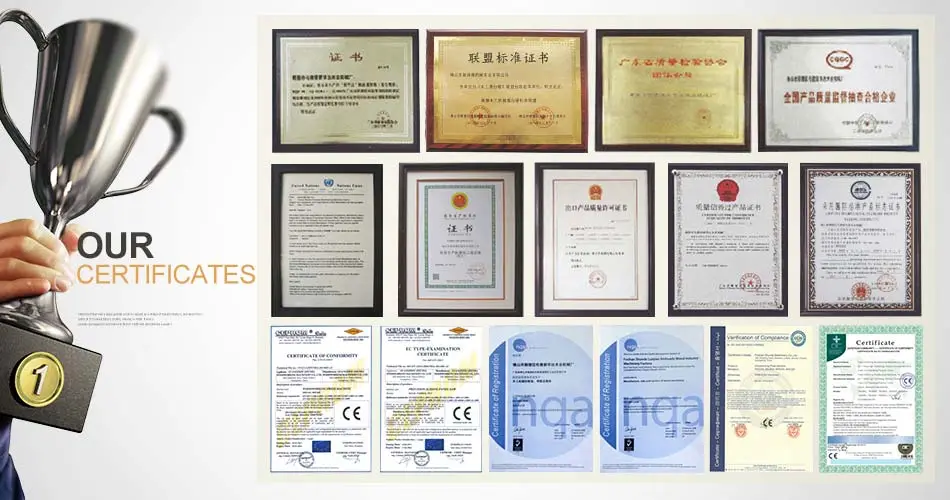
Worktable width (mm) | 1300 ×2500 |
Panel width range(mm) | 1000-1300 |
Splicing thickness (mm) | 8-50 |
Feeding mode | Automatic, stainless steel crawler feeding and discharging |
Upper cylinder pressure (t) | 20 |
Upper cylinder specification (mm) | Φ63*400 |
Number of upper cylinders (single) | 4 |
Side cylinder pressure (t) | 25 |
Side cylinder specification (mm) | Φ40*300 |
Number of side cylinders(single) | 12 |
Rated pressure of hydraulic system (MPa) | 16 |
Outlet mode | Lifting table automatic stacking side discharge |
Total power input power (kVA) | 30 |
High frequency oscillation power (kW) | 20 |
Machine weight(kg) | 10500 |
high frequency machine | Top |
Gluing mode | Two-component side glue |
The pusher of the automatic arrangement machine adopts a servo motor, and the distance and position of the manipulator can be adjusted |